Büscher baut ein komplettes Haus zu 75 % aus recycelten Bau- und Abbruchabfällen. Die primären Rohstoffe für die tragenden und nichttragenden Innenwandelemente bestehen zu 100 % aus Recyclingmaterial.
1961 begann Büscher Beton herzustellen wie jeder andere auch, nämlich aus Kies, Sand, Zement, Zusatzmittel und Wasser. Das Unternehmen hat die Zusammensetzung nun geändert und Sand und Kies vollständig durch gemischte Bau- und Abbruchabfall ersetzt um daraus tragende und nichttragende Betonfertigelemente für Innenwände herzustellen.
Dank des Recyclingunternehmens hat Büscher Zugang zu großen Mengen an Bau- und Abbruchabfällen, die üblicherweise zu Zuschlagstoffen für den Straßenbau recycelt werden. Der Markt für dieses Material ist jedoch sehr gesättigt, sodass die Brüder Wolfgang und Hans-Jürgen Büscher sich auf die Suche nach anderen Verwendungsmöglichkeiten für die großen gelagerten Mengen machten. So kamen sie auf die Idee, es als Sekundärbaustoff nach dem Upcyclingverfahren für Fertigbeton und Betonfertigteile zu verwenden. In Deutschland landen (bis dato) nur <1 % wieder in der Betonherstellung.
8 Jahre Forschungs- und Entwicklungszeit
Es war nicht leicht, Fachwelt und Behörden davon zu überzeugen, dass dies die Zukunft sein könnte. Die Zertifizierung der vollständig aus Recyclingmaterial hergestellten Betonfertigteile war schwierig und nahm 8 Jahre Forschungs- und Entwicklungszeit in Anspruch, weil die Ansprechpartner nicht an diese Lösung glauben wollten. „Betonexperten, Labore und Zertifizierungsfachleute hatten große Zweifel, dass die Lösung funktioniert. Alle waren der Meinung, dass das Verfahren unmöglich und darüber hinaus rechtlich nicht zulässig sei“, so Wolfgang Büscher.
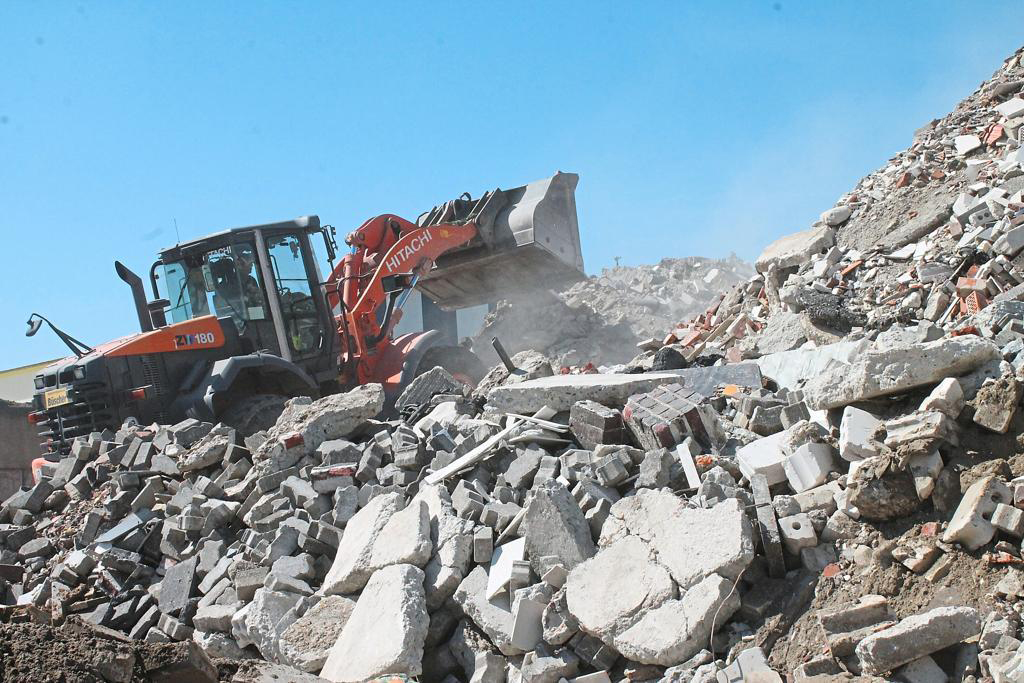
Deshalb wurden Forschungslabore und Universitäten beauftragt, wissenschaftlich zu prüfen, was der Baustoff leisten kann und was nicht. „Alle Studien sind abgeschlossen und haben gezeigt, dass Fertigbeton und Betonfertigteile mit einem Recyclinganteil von 100 % einwandfrei funktionieren, und wir verwenden die Rezeptur inzwischen in der Praxis“, so Hans-Jürgen Büscher.
Prof. Dr.-Ing. Wolfgang Breit von der TU Kaiserslautern kommt zu folgender Einschätzung: „Der Baustoff ist von hoher Qualität, weil man bei Büscher von der Annahme der Bau- und Abbruchabfälle bis zur Verarbeitung zu Fertigbeton und Betonfertigteilen die richtigen Maßnahmen ergriffen hat.“
Kreislauffähig und günstiger als herkömmliche Baustoffe
Der Hauptvorteil dieses zertifizierten Produktionsverfahrens ist der geringe Ressourceneinsatz. Lokal in großer Menge verfügbarer und dadurch schon beim Transport die CO₂-Emissionen senkender Bauschutt wird zu einem nachhaltigen und klimaneutralen Produkt verarbeitet. „Wir wollen unser Verfahren bundesweit bekannt machen und freuen uns, wenn sich auch andere Betonwerke, Recyclingunternehmen und weitere Interessierte zum Thema nachhaltiges Bauen mit Sekundärbaustoffen bei uns melden. Die Bauwirtschaft steht vor einer umfassenden Transformation. Neue Ansätze sind notwendig, damit eingesetzte Baumaterialien nicht als Abfall enden – wir können und dürfen dies mit der Büscher-Wand“, sagt Büscher-Prokurist und Geschäftsleiter Thomas Overbeeke.
Das Unternehmen hat 8 Jahre investiert, um den wissenschaftlichen Nachweis zu erbringen, dass der nachhaltige Bau eines Hauses aus vollständig recyceltem Material möglich ist, und das sogar zu geringeren Kosten als bei Verwendung herkömmlicher Baustoffe. Der Bau eines kompletten Dreifamilienhauses mit den anstrichfertigen Betonfertigteilen hat hingegen nur 4 Monate in Anspruch genommen. Rohrleitungen und Kabel sind bereits in die Betonelemente integriert, und dank ihrer glatten Oberfläche brauchen sie nicht mehr verputzt zu werden. Und wenn das Haus irgendwann einmal abgerissen wird, können die Baustoffe erneut nach dem von Büscher entwickelten Verfahren recycelt werden.
Hochwertige Aufbereitung von Millionen Tonnen Bauschutt denkbar
Allein im Jahr 2018 fielen laut Umweltbundesamt (UBA) aus Bauschutt und Straßenaufbruch 73,9 Mio. t mineralische Abfälle an. Von den recycelten Baustoffen wurden laut UBA jedoch nur 15,8 Mio. t hochwertig in der Asphalt- und Betonherstellung eingesetzt. Technisch ließe sich noch weit mehr Bauschutt aus dem Hochbau wieder für den Hochbau aufbereiten. „Hochgerechnet ließen sich mit den verbliebenen 58,1 Mio. t Bauschutt etwa 375.000 Mehrfamilienhäuser im gleichen „Büscher-Style“ bauen, macht bei 6 Personen je MFH einen neuen Wohnraum für 2.250.000 Menschen innerhalb kürzester Bauzeit (seriell vorgefertigt) und absolut nachhaltig“ fasst Thomas Overbeeke zusammen.
Die Verringerung des eigenen ökologischen Fußabdrucks durch die Schaffung einer Kreislaufwirtschaft ist Büscher jedoch noch nicht genug: Das Betonwerk und der Recyclingstandort des Unternehmens beziehen ihren elektrischen Strom von Solarmodulen. Auch die Entscheidung, Brech- und Siebanlagen von Keestrack zu verwenden, ist aufgrund dieses Ansatzes gefallen. Oppermann & Fuss ist Keestrack-Vertriebspartner in Deutschland und hat Büscher bei der Frage beraten, welche Maschinen der Reihe ZERO und welche optionalen Ergänzungen sich angesichts der beabsichtigten Anwendung und der gewünschten Produktionsleistung am besten für das Unternehmen eignen.